

Wrought Iron had a very low carbon content making it much weaker than steel. The finished ingot, bearing the layers of the folding process, was called “wrought iron”.

This process would continue several more times until most impurities had been driven from the ingot. The bar would be folded over and hammered again. A striker would then hammer the lumpy piece of raw iron into a flat, rectangular bar. Using large tongs, the blooms of iron were pulled from the oven and placed on an anvil. When the temperature rises above 2,800 deg.F, the iron flows from the ore and forms blooms. The furnace was filled with charcoal and iron ore and the charcoal was then set afire.
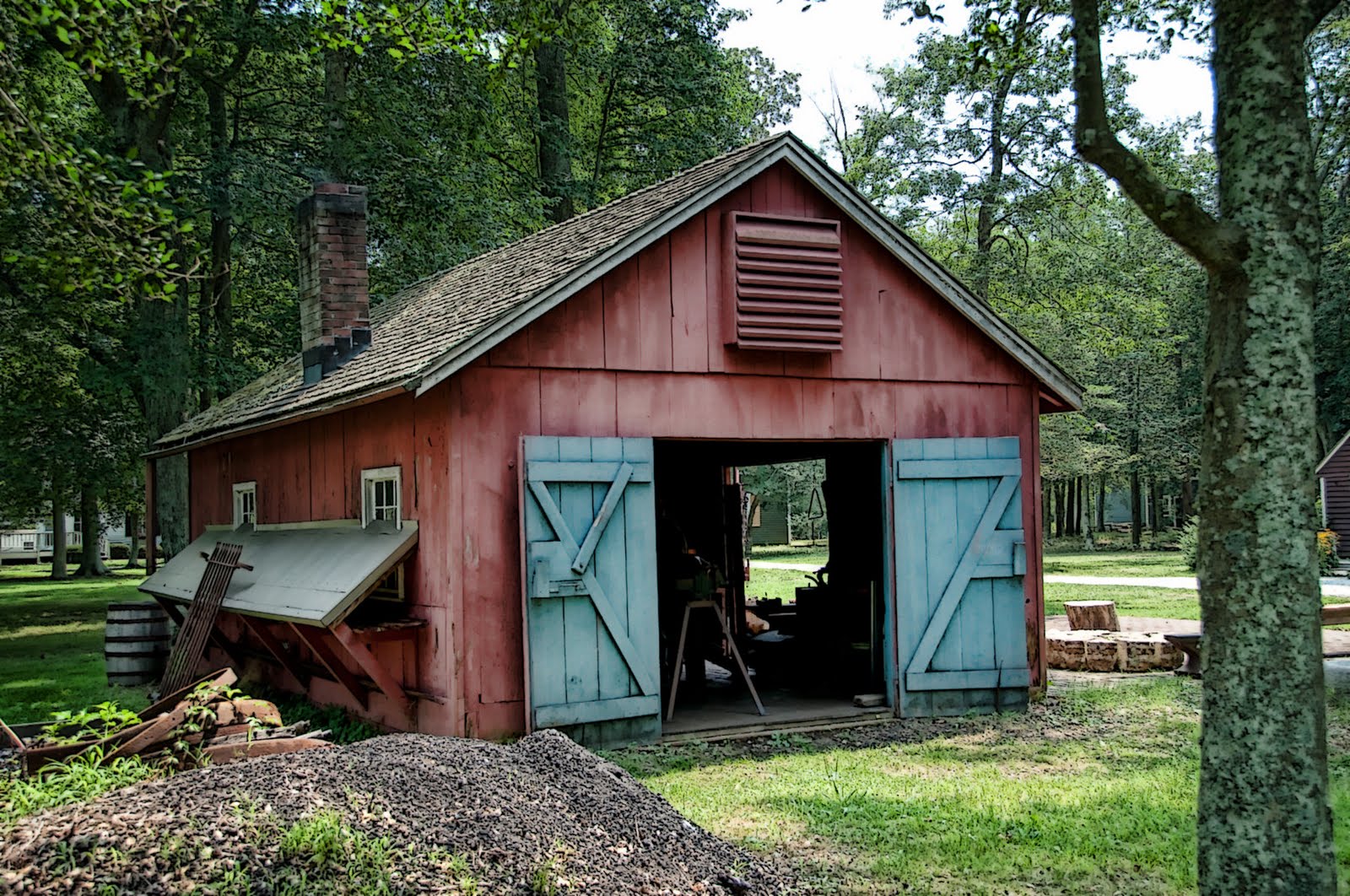
To create the high heat needed to smelt iron, smiths pumped air from a bellows through the tuyere (nozzle). These furnaces looked like beehives with a vent in the top and an entry portal on the side. In early times, that often meant being near a navigable waterway.Įarly iron smelters called “bloomeries” were small furnaces built from rocks that could withstand repeated heating. The ironworks also had to be in an area where transporting the finished iron ingots was practical. Given the weight of the ore and the large amounts of fuel needed to smelt the ore, the earliest ironworks were located in areas where iron, flux, and fuel were ample and in proximity to each other. It became a quest to find the rock strata that gave up its iron with the least amount of work. In addition to charcoal and iron ore, a flux agent (limestone or dolomite) is also needed to smelt iron ore. Beginning in the 18th century, ironworks began converting coal to coke. Iron ore is also present in rock strata that have a red color, and the deeper the red hue, the higher the iron content.Ĭharcoal was the primary fuel for an iron furnace. Iron is also present in nodules of bog ore, small lumps of iron created by bacterial life in swampy areas. Early on, man discovered that small meteorites contain iron. From that point on, sailors could travel without need of stars nor sun to plot their courses around the globe.Īs to where and when blacksmithing evolved depended on fuel and iron ore. By forging the needle as perfectly as he could, the blacksmith aligned the molecules in the iron and that is why north is north and south is south. The first compass used a forged iron needle that floated in a round vial. Long after man made the first simple tools–the first spear or arrow tips–the craft would require hundreds more years before blacksmiths understood the magnetic properties of iron. It took three thousand years for man to learn the science of metallurgy. In short, we can say that blacksmithing, the art of crafting that crude metal into a usable implement, has been around for a long, long time.Īnd for a long time after that, blacksmithing remained a crude art. The Iron Age began when some primitive person noticed that a certain type of rock yielded iron when heated by the coals of a very hot campfire. Blacksmithing began with the Iron Age, when primitive man first began making tools from iron.
